AIRScan - GLobal Airtech Systems
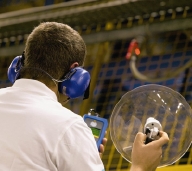
Compressed air is a vital resource in your production process. But it’s also a significant contributor to your power bill: energy accounts for 75% of the lifetime cost of a compressed air system. Another sobering fact is that up to 30% of the energy is wasted. Or in other words, a lot of money disappears into thin air. Atlas Copco has devised AIRScan™ – a highly accurate, independent survey and reporting system to pinpoint the areas where potential savings can be made in your plant. The approach is to first discover exactly where the energy drain originates from and then to take the appropriate actions to remedy or optimize the situation.
AIRScan is not only an accurate compressed air system diagnostics package, it’s very flexible as well. It allows the customer to select the depth of audit required on his particular compressed air network and to tightly control the budget he is willing to allocate to the audit. From a complete audit solution – with an initial baseline audit, a complete evaluation report with solutions, and a final validation –, to individual and specific audit services tailored to the needs of each customer and his installation.
How AIRScan works
Stage 1 – diagnostics check
The initial check-up by our consultant engineers rates the efficiency of your entire compressed air system, including pipework, identifying where energy is being lost and recommended action to saving money. It may be that your system is efficient enough to stop at this point.
Stage 2 – complete system survey
The survey measures, audits and reviews every element of your compressed air system in detail. Yet, despite its thoroughness, in most cases the AIRScan™ survey is non-intrusive and will not require your compressed air system to be shut down.
AIRScan Procedures
1. Air measurement: an accurate account of your plant’s compressed air demand over a 7-day cycle, identifying energy costs and where savings are possible.
2. Air leak detection and control: with leaks typically accounting for 20% of the system demand, this is a critical AIRScan™ function.
3. Air quality audit: measures the quality of the air and compares with your specific needs at any point in your system.
4. Maintenance review: assesses service programme effectiveness for equipment, including compressors, filters, dryers and ancillaries.
5. Monitoring and control programme: sets out recommendations for long-term monitoring and control to maintain optimum efficiency.
6. After completion of an AIRScan™ Diagnostics Check or Complete Survery, you will receive a comprehensive report.
Individual compressed air system checks
Flow check
This test accurately measures and logs the delivered flow of compressed air on any compressor make or type. The flow meter can be inserted into an existing point or the system can be “hot tapped”, without interrupting your production.
Power check
Where other audits use clamps or rely on the customer’s originally installed power meters to estimate power usage, Atlas Copco’s method measures the actual consumed power, non-intrusively.
This check is available for all types of compressors over a predetermined period, usually 7 days. The results give an accurate overview of the money you are spending annually on the production of compressed air.
Leak check
Compressed air leakage is synonymous for evaporating money! Between 10 and 25% leakage is typical in most systems. Atlas Copco’s leak check identifies, tags and quantifies these leaks throughout your compressed air system. To immediately start saving money, repairs can be performed during the audit.
AIRScan – tangible information for real solutions
A complete AIRScan audit includes a full survey of important compressed air net parameters, and the solutions that emerge from it. Using the logged information, a detailed report is compiled, including cost analysis, graphs and a list of recommendations for improving your system’s performance.
The sooner you act, the sooner you start saving.
Make a decision on AIRScan™ now and you could be making a real contribution to your bottom line – both now and in the long term. Contact your local Atlas Copco expert or go for an energy optimization contract.